Good quality QT4-15B cement block machine/concrete block machine/fly ash block machine
1. The QT4-15B cement block machine is equipped with the touch-screen computer. The Japanese Mitsubishi PLC control system allows the full automation and intellectualization of the production process, including blending, material feeding, and compression molding. Each plate can make four air bricks, or 28 to 30 pieces of standard bricks.
2. Concrete block machine is made of super strong structural steel via the special welding technique and welding materials. This block machine applies the imported motors, sealing elements, and hydraulic components. Therefore, it is durable and shock proof. That is to say, our machine features stable and reliable performance.
3. In addition to the overlong sliding sleeve, four guide pillars are also used to make the pressure head and mould move accurately. The uplink synchronous device is utilized.
4. Our fly ash block machine applies the large-scale hydraulic machinery used oil jack to press from up and down. Hence, it can make the heavy bricks with the maximum intensity up to 20Mpa. Those finished products enjoy the advantages of good compactness, accurate size.
5. It has two types of stacker cranes for you to choose. The block machine is multi-fuctional, since it can make the blocks of any materials. It can make numerous different blocks when equipped with different molds.
Each part introduction
Batching Plant: : This is the starting point of the Production process. It consists of three loading bins and one weighing bin. It also contains blet conveyers to convey materials from loading bins to weighing bin. Batching and weighing is done by PLC control. We can load three different types of material into the loading bin.
Screw Conveyer (Optional fitment): Loading bins of the This is instrumental for transporting Fly Ash from the silos(optional fitting) or cement hopper (optional fitting) to the Batching Plant.
Conveyer Belt: When the Batching plant's weighing bin trips according to the PLC control, the material comes to this conveyer belt. The material is then carried to the Mixture Machine.
Concrete Mixture Machine: All the ingredients are mixed in this mixture machine. The mixing time and speed is controlled by PLC. The inbuilt water pump adds water to the mix automatically, as per requirement.
Theoretical workshop area : 15 0m 2 , need about 6-7 workers .the office , curing area and stacking area to arrange according your fact status..
(2) Production capacity
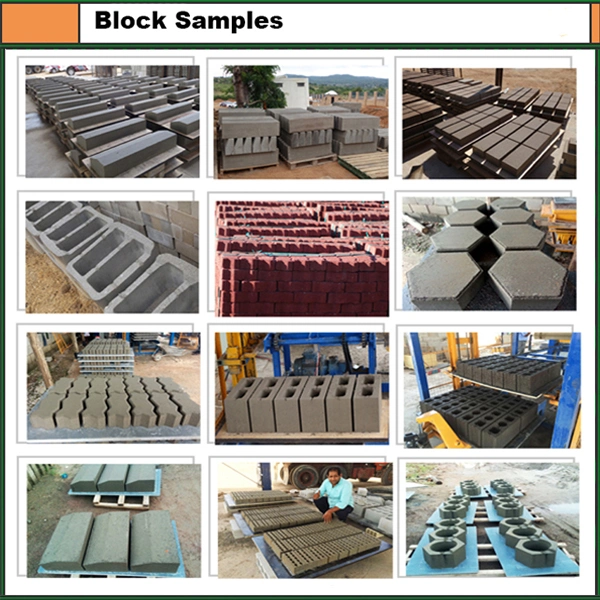
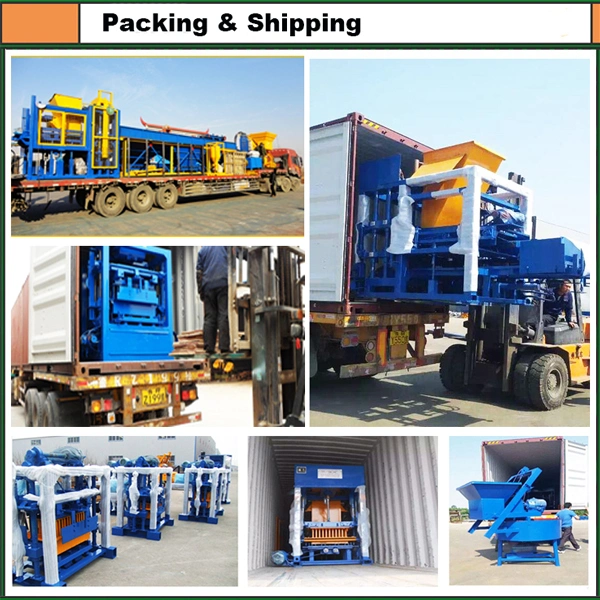
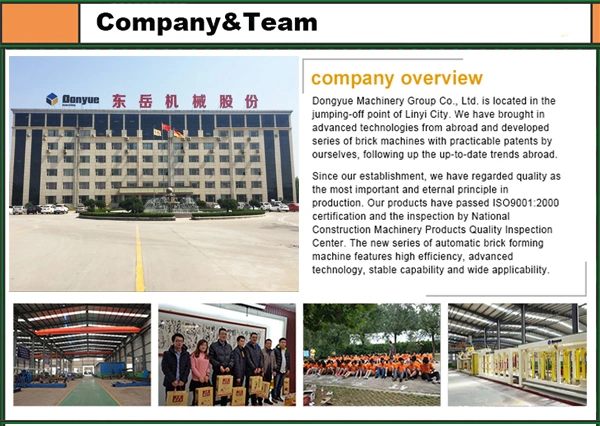
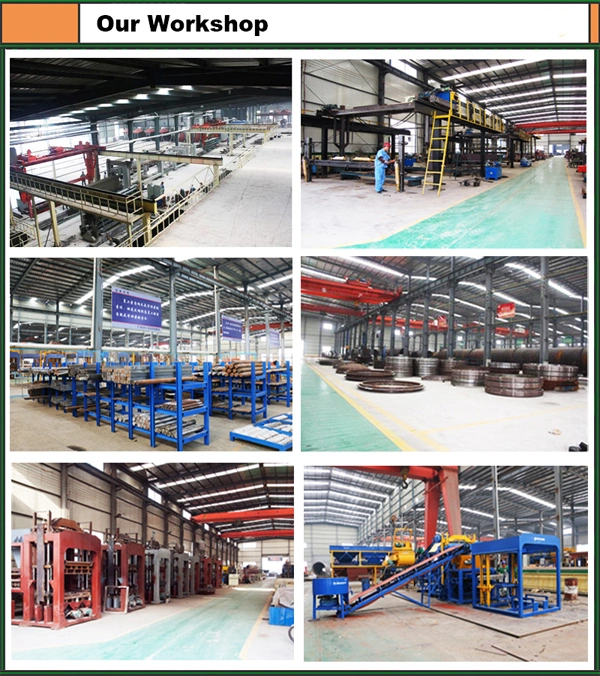
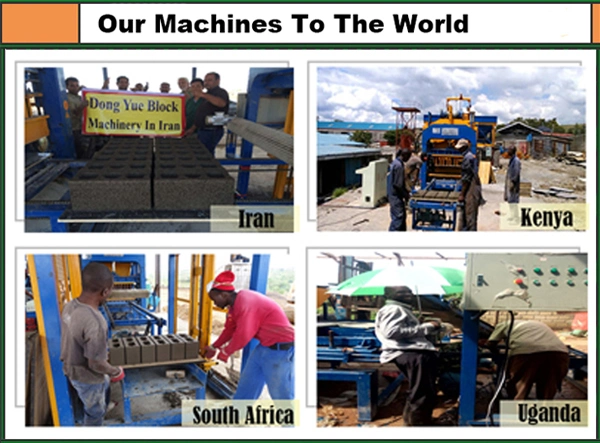
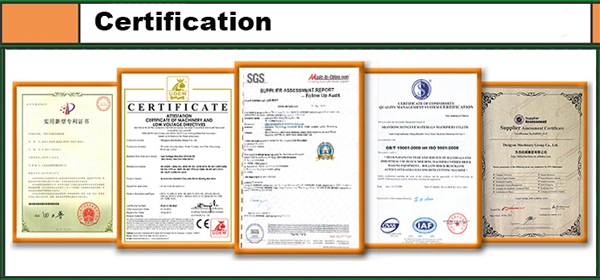
1. The QT4-15B cement block machine is equipped with the touch-screen computer. The Japanese Mitsubishi PLC control system allows the full automation and intellectualization of the production process, including blending, material feeding, and compression molding. Each plate can make four air bricks, or 28 to 30 pieces of standard bricks.
2. Concrete block machine is made of super strong structural steel via the special welding technique and welding materials. This block machine applies the imported motors, sealing elements, and hydraulic components. Therefore, it is durable and shock proof. That is to say, our machine features stable and reliable performance.
3. In addition to the overlong sliding sleeve, four guide pillars are also used to make the pressure head and mould move accurately. The uplink synchronous device is utilized.
4. Our fly ash block machine applies the large-scale hydraulic machinery used oil jack to press from up and down. Hence, it can make the heavy bricks with the maximum intensity up to 20Mpa. Those finished products enjoy the advantages of good compactness, accurate size.
5. It has two types of stacker cranes for you to choose. The block machine is multi-fuctional, since it can make the blocks of any materials. It can make numerous different blocks when equipped with different molds.
Each part introduction
Batching Plant: : This is the starting point of the Production process. It consists of three loading bins and one weighing bin. It also contains blet conveyers to convey materials from loading bins to weighing bin. Batching and weighing is done by PLC control. We can load three different types of material into the loading bin.
Screw Conveyer (Optional fitment): Loading bins of the This is instrumental for transporting Fly Ash from the silos(optional fitting) or cement hopper (optional fitting) to the Batching Plant.
Conveyer Belt: When the Batching plant's weighing bin trips according to the PLC control, the material comes to this conveyer belt. The material is then carried to the Mixture Machine.
Concrete Mixture Machine: All the ingredients are mixed in this mixture machine. The mixing time and speed is controlled by PLC. The inbuilt water pump adds water to the mix automatically, as per requirement.
Dimension of host machine | 2440×2000×2600mm | Host machine power | 27KW |
Moulding area | 400×800mm | Vibration force | 40KN |
Moulding period | 15-20S | Capacity | 70.25KVA |
The size of the pallet | 1010×550×20/25mm | Mixer model | JS500 |
Weight of the host machine | 7.6T | General water Consumption | 5T/every day |
Voltage | 380V |
(2) Production capacity
Size(LxWxH) | Pcs/Mould | Pcs/ Hr | Pcs/ 8 Hr | m3/year |
400X100X200 | 8 | 1200-1920 | 9600-15360 | 27648-36864 |
400X150X200 | 6 | 900-1440 | 7200-11520 | 31104-41472 |
400X200X200 | 4 | 600-960 | 4800-7680 | 27648-36864 |
400X250X200 | 3 | 450-720 | 3600-5760 | 25920-34560 |
Paver:200X100X60 | 16 | 1920 | 15360 | |
Paver:200X163X60 | 8 | 1200 | 9600 |
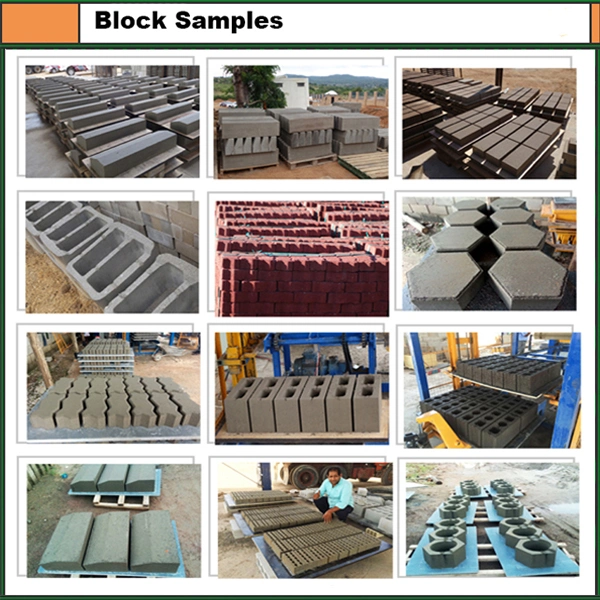
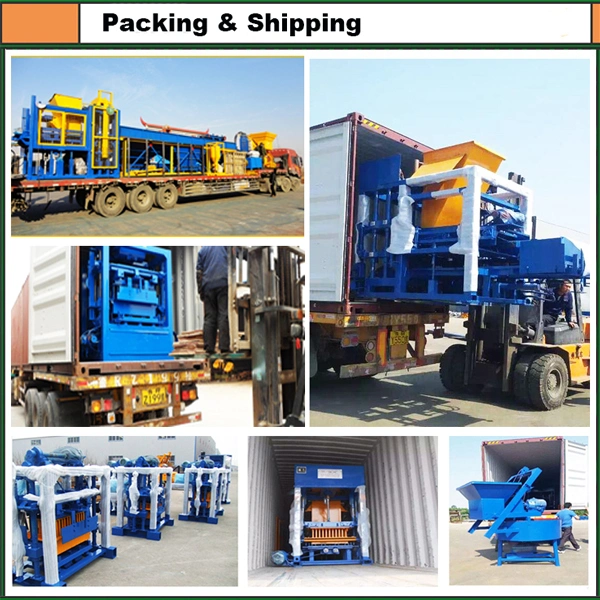
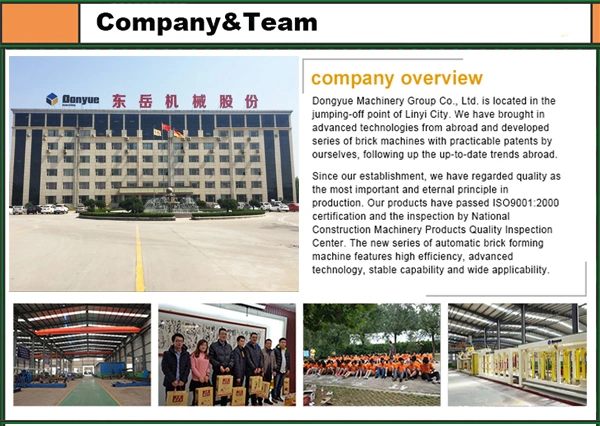
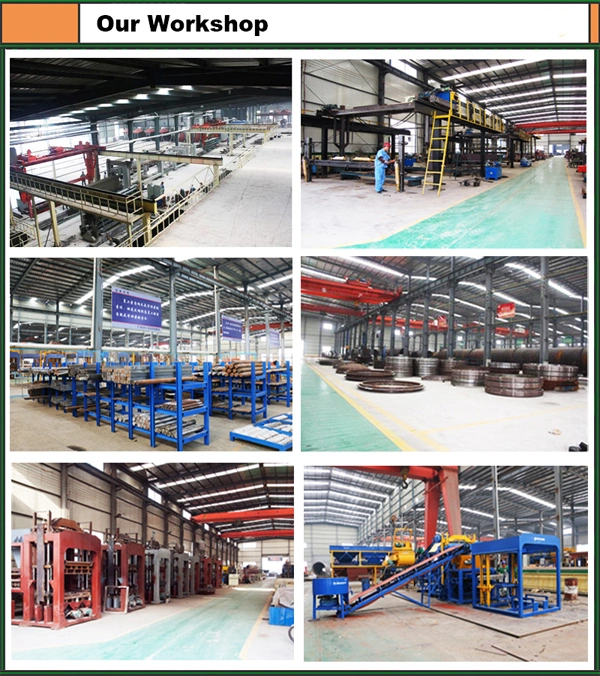
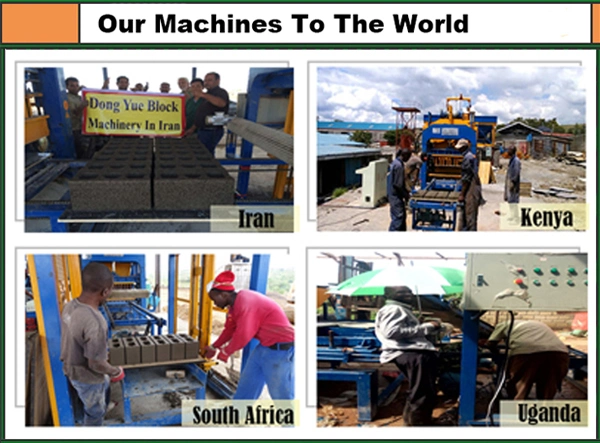
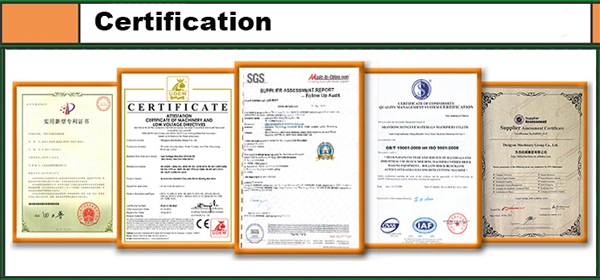